Прецизійні металеві деталі часто виготовляються з використанням різних технологій прецизійної обробки, поширеним методом є обробка на верстатах з ЧПК. Зазвичай прецизійні деталі вимагають високих стандартів як щодо розмірів, так і зовнішнього вигляду.
Тому під час обробки металів, таких як алюміній та мідь, на верстатах з ЧПК виникає занепокоєння щодо появи слідів та ліній від інструменту на поверхні готового виробу. У цій статті розглядаються причини, що викликають появу слідів та ліній від інструменту під час обробки металевих виробів. Ми також пропонуємо потенційні рішення.
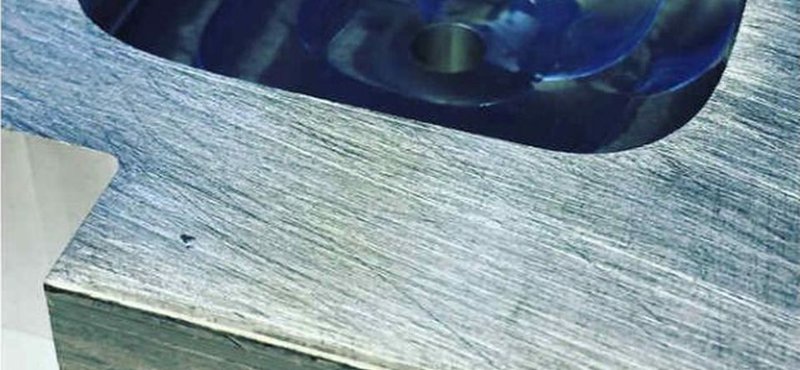
Недостатня сила затиску світильників
Причини:Для деяких металевих виробів з порожнинами потрібно використовувати вакуумні пристосування, і їм може бути важко створити достатнє всмоктування через наявність нерівностей поверхні, що призводить до появи слідів або ліній від інструменту.
Рішення:Щоб пом'якшити це, розгляньте перехід від простого вакуумного відсмоктування до вакуумного відсмоктування в поєднанні з тиском або бічною опорою. Або ж дослідіть альтернативні варіанти кріплення на основі конкретних конструкцій деталей, адаптуючи рішення до конкретної проблеми.
Фактори, пов'язані з процесом
Причини:Певні виробничі процеси можуть сприяти цій проблемі. Наприклад, такі вироби, як задні панелі планшетних ПК, проходять послідовність етапів обробки, що включає пробивання бічних отворів, а потім фрезерування країв на верстаті з ЧПК. Ця послідовність може призвести до помітних слідів інструменту, коли фрезерування досягає положень бічних отворів.
Рішення:Поширений випадок цієї проблеми виникає, коли для корпусів електронних виробів вибирається алюмінієвий сплав. Щоб вирішити цю проблему, процес можна модифікувати, замінивши бокове пробивання отворів плюс фрезерування лише фрезеруванням на верстаті з ЧПК. Одночасно це забезпечує стабільне зачеплення інструменту та зменшує нерівномірність різання під час фрезерування.
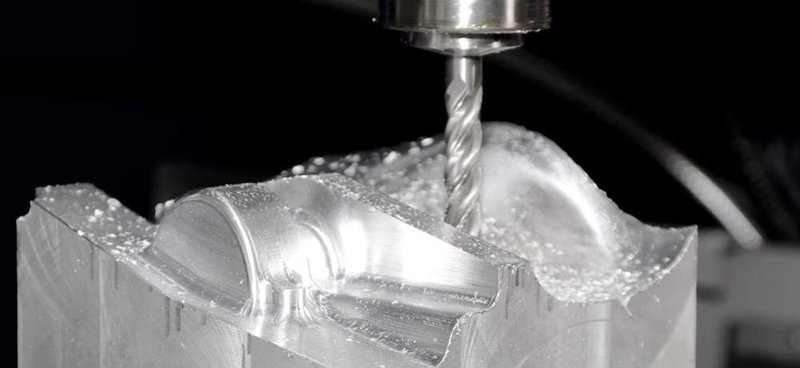
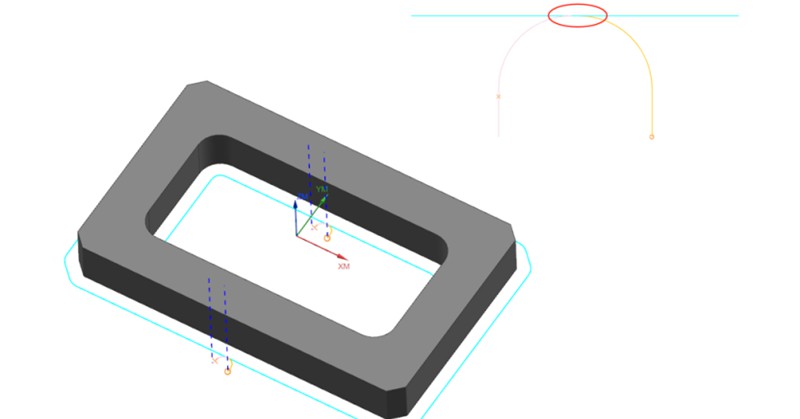
Недостатнє програмування зачеплення з траєкторією інструменту
Причини:Ця проблема зазвичай виникає під час фази 2D-контурної обробки виробу. Погано розроблена траєкторія руху інструменту в програмі ЧПК, що залишає сліди в точках входу та виходу інструменту.
Рішення:Щоб вирішити проблему уникнення слідів інструменту в точках входу та виходу, типовий підхід передбачає невелике перекриття відстані зачеплення інструменту (приблизно 0,2 мм). Цей метод служить для уникнення потенційних неточностей у точності ходового гвинта верстата.
Хоча ця стратегія ефективно запобігає утворенню слідів від інструменту, вона призводить до повторюваної обробки, коли матеріал виробу – м’який метал. Отже, ця ділянка може демонструвати відмінності в текстурі та кольорі порівняно з іншими ділянками.
Візерунки риб'ячої луски на плоских оброблених поверхнях
Причини:На плоских поверхнях виробу з'являється риб'яча луска або круглі візерунки. Різальні інструменти, що використовуються для обробки м'яких металів, таких як алюміній/мідь, зазвичай є фрезами для сплавів з 3-4 зубцями. Вони мають твердість від HRC55 до HRC65. Ці фрезерні різальні інструменти виконуються за допомогою нижнього краю інструменту, і поверхня деталі може мати характерні візерунки риб'ячої луски, що впливає на її загальний вигляд.
Рішення:Зазвичай спостерігається у виробах з високими вимогами до площинності та на плоских поверхнях із заглибленими структурами. Рішенням є перехід на ріжучі інструменти, виготовлені з синтетичного алмазного матеріалу, що допомагає досягти більш гладкої обробки поверхні.
Старіння та знос компонентів обладнання
Причини:Сліди інструментів на поверхні виробу пояснюються старінням та зносом шпинделя, підшипників та ходового гвинта обладнання. Крім того, недостатні параметри люфту системи ЧПК сприяють вираженим слідам інструментів, особливо під час обробки закруглених кутів.
Рішення:Ці проблеми виникають через фактори, пов'язані з обладнанням, і їх можна вирішити шляхом цілеспрямованого технічного обслуговування та заміни.
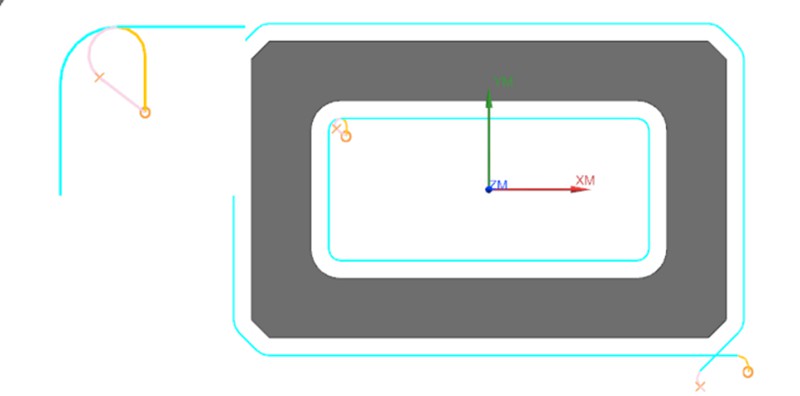
Висновок
Досягнення ідеальної поверхні при обробці металів на верстатах з ЧПК вимагає корисних підходів. Існують різні методи уникнення слідів та ліній від інструменту, які включають поєднання технічного обслуговування обладнання, удосконалення пристосувань, налаштування процесу та вдосконалення програмування. Розуміючи та виправляючи ці фактори, виробники можуть гарантувати, що прецизійні компоненти не лише відповідають розмірним критеріям, але й мають бажані естетичні якості.